3D Printer Innovation: Aurora Labs Unveils the AL250
- Alexander Fäh
- Oct 10, 2023
- 2 min read
Aurora Labs introduces the AL250 3D printer, offering innovative technologies for additive manufacturing, including bidirectional powder bed recoating and a unique powder dosing mechanism.
The AL250 is capable of producing high-quality and repeatable assemblies, expanding its applications across various industries such as defense, aerospace, and oil and gas.
This printer will serve as a key tool for prototype development and mass production of custom parts, significantly enhancing the possibilities of additive manufacturing.
Aurora Labs Introduces AL250 3D Printer with Groundbreaking Technologies.
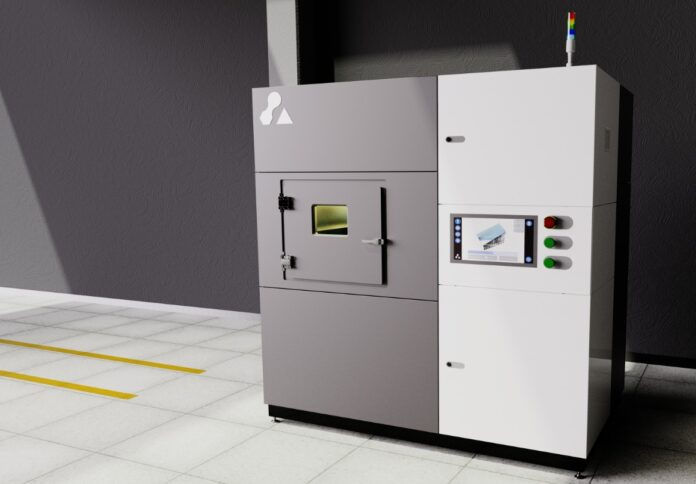
ASX-listed 3D printing company Aurora Labs has unveiled its new AL250 commercial printer project, marking a significant transition from the RMP-1 printer model to the newly designed AL250 laser powder bed fusion machine.
In a media release, the company said the AL250 is poised to become an essential component of the company’s printing bureau, offering a wide range of technical capabilities.
Additionally, it will serve as a demonstration model for potential customers interested in future machine acquisitions.
The AL250 boasts several key technical attributes that set it apart in the field. Notably, it incorporates bidirectional recoating of the powder bed, powered by MCP technology.
This approach not only reduces recoat time but also enhances cost efficiency by allowing for extended laser exposure times, the company said.
This feature also empowers the rapid and cost-effective prototyping and serial production of industrial products, particularly custom parts or components that were previously unattainable through conventional manufacturing methods.
Integral to the AL250’s functionality is its unique powder dosing mechanism. This mechanism preconditions the powder with heat before depositing it into the recoating system, ensuring that powders maintain optimal temperatures for spreading and densification during the powder layer formation process.
Consistency in powder layering reduces mechanical defects within parts, guaranteeing the production of high-quality, repeatable builds.
Moreover, the AL250 comes equipped with a build plate heater capable of reaching 200 degrees Celsius, enhancing its capabilities in materials research. Strict environmental control measures enable precise monitoring of gas flow, recirculation, temperature, and humidity within the build chamber during the printing process.
The AL250 features a formidable lasing power of 1500W per laser, making it suitable for processing highly reflective or conductive powders like copper.
The machine also offers efficient and optimized process parameters for handling a variety of powder materials, making it a versatile addition to the world of additive manufacturing.
The AL250 printer is aimed at a diverse range of industries, including defense, aerospace, oil and gas, engineering experts, and OEMs with extensive collections of custom-made parts.
Aurora Labs said demonstrating the printer’s capabilities to address intricate challenges through generative design and AL250 printing will be essential in showcasing its versatility and power to a broader audience.