Guatemala's First 3D-Printed Earthquake-Resistant Dwelling with an Unusual Element
- Alexander Fäh
- Nov 2, 2023
- 2 min read
Das erste 3D-gedruckte Tiny House in Guatemala setzt auf Palmblätter, um seismischen Aktivitäten standzuhalten.
COBOD, der Maschinenhersteller, hat weltweit über 70 seiner Bauprintersysteme verkauft und wurde bereits für Projekte in Madagaskar, Kenia und Guatemala verwendet.
3D-Druck-Technologie ermöglicht eine schnellere und kostengünstigere Bauweise, könnte jedoch in Zukunft noch preiswerter werden.
Palm Leaves as a Secret Weapon: Guatemala's First 3D-Printed Earthquake-Resistant Dwelling.
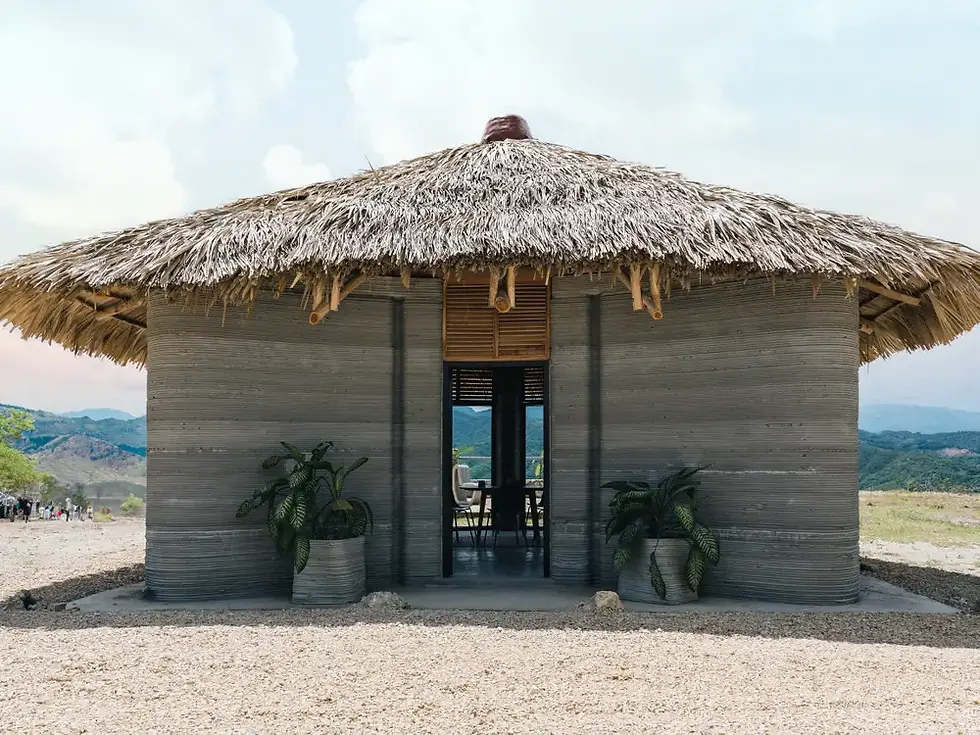
The companies behind Guatemala's first 3D-printed tiny home say this 527-square-foot unit has one secret element that helps it withstand seismic activities — palm leaves.
Over the last few years, more US startups and real estate companies have been turning to 3D printing construction methods. And progress is happening fast — this year, the first batch of residents are expected to move into a first-of-its-kind 100-home printed community near Austin, Texas.
Internationally, this homebuilding tech is finding footing as well. In 2022, a nonprofit unveiled a $300,000 3D-printed school in Madagascar. More recently in July, a Japanese company printed a 527-square-foot tiny-home prototype for about $37,300. And in Kenya, 14Trees is currently using this process to create a community of 52 homes.
Now, the global 3D printing community is welcoming one of its newest builds: an earthquake-resistant tiny home in Guatemala. According to the printer's manufacturer COBOD, this project is the Central American country's first 3D-printed home.
COBOD has sold over 70 of its "BOD2" construction printer systems to companies around the world. You may recognize some of the projects it's been used for, including the aforementioned Madagascan school, Kenyan community, and now this Guatemalan home.
Using this tech, the new home's nine-foot-tall walls were printed in 26 hours over a week while completion on the rest of the home "took longer than printing," Philip Lund-Nielsen, COBOD's cofounder, told Insider. To make it 9.0-magnitude earthquake-resistant — according to his LinkedIn post — the unit was topped with a traditional palm leaf-based thatched roof "ideal for seismic regions," as per COBOD's release.
But because the Denmark-headquartered company is just the equipment manufacturer, it wasn't directly involved in the execution of this home. Instead, it was headed by cement company Progreso and 3D printing construction establishment 3DCP Group. The former purchased its COBOD printer at least a year ago with this tiny home being its first demo project, Lund-Nielsen said. Meanwhile, the latter has been involved in projects like a 400-square-foot concrete home completed in five weeks.
Proponents of 3D printing construction say the tech can build homes faster and cheaper with less waste and labor. At this point, Lund-Nielsen says the price of using printers is "on par or a bit more expensive" than conventional construction methods. (He couldn't confirm to Insider the budget of this Guatemala project). However, he believes this cost will decrease as the tech continues to advance, likening this progression to the history of mobile phones.
"I hope that in decades from now, there'll be 3D printers on most construction sites around the globe," Lund-Nielsen said.