Revolution in the Gas Sector: Upwing Energy Utilizes 3D Printing for Groundbreaking Compressor Technology
- Alexander Fäh
- Dec 21, 2023
- 1 min read
Upwing Energy pioneers 3D printing technology with Velo3D for innovative gas compressors.
3D printing not only saves time but allows for intricate designs and improved performance.
Metal 3D printing revolutionizes the gas industry by producing highly precise and durable parts for demanding applications.
Advancing Innovation with 3D Printing: Upwing Energy Partners with Velo3D for Pioneering Gas Compressor.
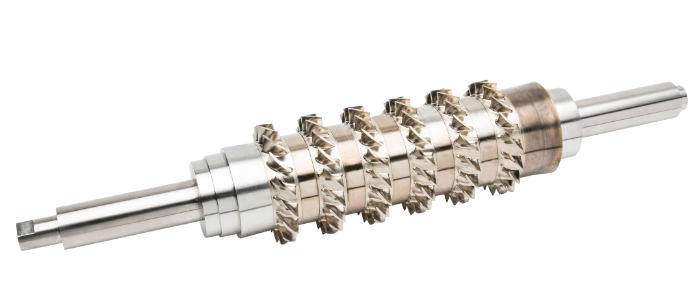
US-based natural gas service provider Upwing Energy has successfully leveraged Velo3D's Laser Powder Bed Fusion (LPBF) 3D printing technology to produce the compressor module of its Subsurface Compressor System (SCS).
By using Velo3D’s 3D printer, Upwing reduced manufacturing time, enabling the company to go from engineering design to full compressor rotor assembly production in just 10 weeks. Tests simulating gas compression conditions highlighted the high quality and durability of the 3D printed parts.
"All of our work at Upwing is underscored by the belief that continuous improvement is always possible," commented Robert McKeirnan, Vice President of Supply Chain and External Manufacturing at Upwing Energy. "Our decision to integrate additive manufacturing makes us more scalable and adaptable. It allows us to create parts that are not only durable but intricately designed and finished with the highest level of precision."
Manufactured from Inconel 718, Upwing’s proprietary SCS compressor module is designed to increase the production and recoverability of natural gas from existing wells. The SCS features a multistage hybrid axial compressor, boosting drawdown at the intake and pressure at the discharge.
In addition to significant lead time savings, Velo3D’s metal 3D printing technology enables the creation of more intricate designs than conventional manufacturing methods. The 3D printed components feature geometric and material benefits, resulting in improved performance and increased part lifecycle.