TRUMPF Reduces CO2 Emissions with 3D Printing for Sustainable Production
- Alexander Fäh
- Nov 1, 2023
- 2 min read
TRUMPF employs 3D printers to reduce CO2 emissions and produce sustainable serial parts.
C.HAFNER utilizes TRUMPF printers for the eco-friendly recycling of precious metal-containing secondary materials.
The new TruPrint 2000 enables energy-efficient serial part production and CO2 reduction.
3D Printing Innovation: TRUMPF and C.HAFNER Set the Bar for Sustainability.
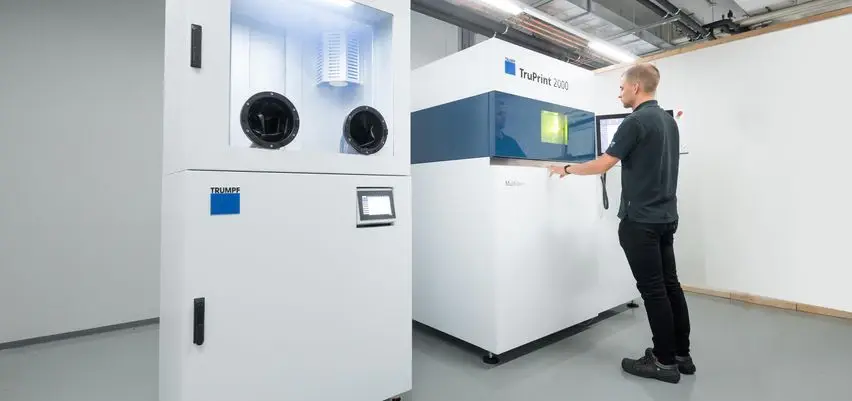
The renowned company TRUMPF actively contributes to reducing CO2 emissions by integrating 3D printers into its manufacturing processes. This innovative technology enables cost-effective production of serial parts and supports the company's commitment to climate protection. TRUMPF showcases sustainably manufactured components at the Formnext trade fair in Frankfurt, the world's leading 3D printing event.
C.HAFNER also relies on TRUMPF's 3D printers for the sustainable production of components. The company recycles precious metal-containing secondary materials and uses them to produce electrodes and watch cases.
Additive manufacturing with TRUMPF printers allows significant energy savings and a substantial reduction in CO2 emissions. Thanks to 3D printing, parts can be manufactured close to their final form, reducing material consumption and eliminating the need for tooling.
TRUMPF itself benefits from 3D printing to make serial part production more sustainable. An impressive example is the production of motor coolers for lasers, where CO2 emissions per produced part were reduced by 83 percent compared to conventional manufacturing. Instead of multiple individual pieces that had to be procured and assembled individually, a 3D printer produces 47 motor coolers in a single printing process.
At the Formnext trade fair, TRUMPF presents the new TruPrint 2000. This 3D printer features a larger build space compared to the previous version, enabling the production of more parts in a single print run.
Despite increased productivity, energy consumption remains consistently low. A remarkable case is the production of dental prostheses, where energy consumption per manufactured part was reduced by more than 50 percent.
With the new TruPrint 2000, TRUMPF also introduces an innovative gas filtration system that reduces the number of components to be disposed of when replacing the filter element.